3.1.1. Диагностика дефектов подшипников качения
Русов В.А.
"Диагностика дефектов вращающегося оборудования по вибрационным сигналам" 2012 г.
3.1. Диагностика дефектов уровня «подшипник»
К уровню «подшипник» относятся все дефекты опорных подшипников агрегатов, и самих опорных стоек. Поскольку наибольшее распространение в практике нашли подшипники качения и скольжения, в данном разделе рассматриваются особенности диагностики дефектов именно этих типов подшипников.
Подшипники качения различных типов и марок, шариковые и роликовые, радиальные и радиально - упорные, однорядные и двухрядные и т. д. широко применяются во вращающемся оборудовании различного назначения. Без преувеличения можно сказать, что большая часть ремонтов оборудования, особенно малой и средней мощности, производится по причине дефектов опорных подшипников качения. Поэтому вопросы оперативной оценки технического состояния таких подшипников, диагностики возникающих в них дефектов, а также прогнозирования возможности их дальнейшей эксплуатации, занимают одно из самых важных мест в работе служб вибрационной диагностики.
В данной главе сделан достаточно краткий обзор основных диагностических методов, применяемых для оценки качества подшипников, определения дефектов на различных стадиях развития, расчета остаточного ресурса подшипников качения. Причина краткости описания проста - каждый из перечисленных ниже методов требует для своего полного описания отдельной книги.
3.1.1.1. Основные признаки и особенности развития дефектов
Наличие дефекта в подшипнике качения легко выявляется несколькими способами. Дефект может быть диагностирован «на слух», по форме вибрационного сигнала, по спектру, по СКЗ сигнала, по спектру огибающей вибрационного сигнала, с использованием «пик-фактора», «эксцесса», и другими методами.
Во вступительном разделе мы рассмотрим различные особенности и признаки возникновения, развития и диагностики дефектов подшипников качения, акцентируя внимание на тех особенностях, которые нам понадобятся далее, для описания того или иного метода диагностики подшипников. Это позволит уменьшить дублирование описательной информации, которую необходимо приводить при описании каждого метода диагностики дефектов.
Характерная форма вибрационного сигнала, в данном случае, зарегистрированного на опоре с подшипником качения, имеющем достаточно развитый дефект состояния, для примера, приведена на рисунке 3.1.1.1. На этом рисунке хорошо видны две наиболее характерные, и важные для диагностики, составляющие сигнала вибрации – фоновая, и импульсная.
Фоновое,
или среднее значение уровня вибросигнала, регистрируемого на подшипнике
качения, характеризуется каким - то усредненным значением, например среднеквадратичным
значением виброскорости. Это значение вибрации достаточно просто может быть замерено
при помощи обычных виброметров.
В моменты прохождения через «несущую», нагруженную зону подшипника качения, дефектного элемента, или элементов, на вибросигнале появляется четко выраженный амплитудный пик, некий энергетический импульс. Параметры этого импульса определяются видом, локализацией и степенью развития дефекта подшипника. Каждый такой ударный импульс обладает четырьмя основными диагностическими параметрами. Это максимальная амплитуда импульса, частота свободных (заполняющих) колебаний, скорость затухания амплитуды этих колебаний, и частота повторения импульсов.
Наиболее важным параметром, характеризующим степень развития дефекта подшипника, является амплитуда ударного импульса. Для измерения этого параметра импульса в приборах вибрационного контроля должны быть предусмотрено использование высокочастотных датчиков измерения вибрации и применения специальных пиковых детекторов или достаточно высокочастотных АЦП. Это обусловлено тем, что ударные импульсы имеют сравнительно высокую частоту. Локализация дефекта, место его расположения, обычно уточняется по частоте следования импульсов, для чего используются спектральные методы.
Если
диагностику состояния опорных подшипников качения проводить по параметрам
временных вибрационных сигналов, то основное внимание следует уделить двум.
Это, во-первых, количественное значение общего уровня фона вибрации и, измеренное
лучше в размерности СКЗ, во-вторых, это соотношение между уровнями фона
вибрации и амплитудами пиковых значений в вибрационном сигнале.
В самом общем случае изменение технического состояния подшипника качения, возникновение и развитие в нем дефектов, за весь период его службы можно, разделить на пять основных этапов. Эти этапы схематически показаны на рис. 3.1.1.2. На этом рисунке по вертикали отложен уровень вибрации в размерности виброскорости (мм/сек), а по горизонтальной оси отложено относительное время эксплуатации подшипника.
Обобщенное техническое состояние подшипника, на каждом этапе его эксплуатации, определяется зоной между двумя линиями вибрационных уровней. Нижняя линия соответствует значению фонового уровня вибрации, определенному в размерности СКЗ виброскорости, а верхняя линия соответствует усредненной амплитуде ударных импульсов, возникающих при работе подшипника качения.
Как мы уже отмечали, этапов, характеризующих изменение технического состояния подшипников качения, можно выделить пять. На первом этапе, на рисунке это зона до границы с отметкой «1», общее техническое состояние подшипника будем считать идеальным. Эту зону можно считать не зоной наличия дефектов, а зоной их первичного возникновения. Дефекты еще не оказывают влияния на вибрации подшипников, все имеющее место увеличение вибрации обусловлено естественным износом поверхностей качения подшипников. На этом этапе пики вибрации превышают уровень фона незначительно, а сам «фоновый уровень» вибрации, в данном случае это СКЗ виброскорости, значительно меньше нормируемых значений тревожного и аварийного уровней, принятых для данного класса оборудования.
Зона «1-2» на рисунке 3.1.1.2. В этой зоне, начиная с границы «1», в подшипнике появляется и начинает развиваться какой-либо дефект, который сопровождается ударными вибрационными импульсами, амплитуда который быстро растет по величине. «Разрушающая энергия» импульсов затрачивается на «углубление» дефекта в рабочих поверхностях подшипника, в результате чего происходит еще большее увеличение энергии импульсов. Уровень фона вибрации по своей величине при пока этом почти остается неизменным, т. к. дефект носит локальный характер и на общем состоянии подшипника пока не сказывается. Повторим, что это зона возникновения дефекта в процессе эксплуатации.
Зона «2-3». Начиная с границы «2» ударные импульсы в подшипнике достигают по своей энергии, применительно к графику это увеличение по амплитуде, практически максимального значения. Дальше амплитуда импульсов уже растет немного. Количественное значение максимума энергии импульсов определяется типом подшипника и условиями его эксплуатации. Выделяющаяся в подшипнике энергия импульсов уже столь велика, что ее достаточно не только «для углубления», но и для расширения зоны дефекта. На данной стадии процесс саморазвития дефекта начинает идти более быстро. Одновременно с этим и уровень фона тоже растет достаточно монотонно. Можно сказать, что дефект набирает силу, готовиться к решающему нападению.
Зона «3-4». Это зона перехода дефекта подшипника от стадии «сильный дефект» к полной деградации. Процесс начинается с границы «3». Геометрическая зона развития дефекта здесь уже столь велика, что подшипник начинает «терять» свое основное назначение - обеспечивать вращение поддерживаемого вала с минимальным трением. Возрастают потери в подшипнике на вращение ротора и, как результат, увеличивается энергия, выделяющаяся в подшипнике, растет уровень фона. Это уже этап саморазрушения подшипника.
Зона «4-5». Это последний этап развития дефекта, когда он охватил уже весь подшипник, вернее говоря все то, что осталось от подшипника. Уровень фона вибрации практически сравнялся с уровнем пиков, точнее говоря, весь вибрационный сигнал состоит из пиков. Работы подшипников качения в этой зоне следует избегать, хотя, если говорить точнее, она уже просто невозможна.
Все эти вышеперечисленные этапы ухудшения состояния подшипника свойственны практически всем видам дефектов, имеющих место в любых разновидностях подшипников. В зависимости от ряда конструктивных и эксплуатационных параметров подшипников могут наблюдаться различия в длительности описанных этапов, в интенсивности вибрационных процессов в них, но общая картина развития дефектов не меняется.
Есть и другие характерные признаки наличия дефектов в подшипниках качения.
При работе подшипника с дефектами на поверхностях качения в спектре вибрационного сигнала появляются характерные составляющие, гармоники, с собственными частотами, по которым можно достаточно корректно выявить место нахождения дефекта. Численные значения частот этих гармоник зависят от соотношения геометрических размеров элементов подшипника, и конечно однозначно связаны с оборотной частоты вращения ротора контролируемого механизма.
В нагруженном подшипнике качения можно дифференцировать четыре основные, характерные, применяемые для диагностики частоты - гармоник. Это гармоники (от оборотной частоты) вызываются специфическими процессами на внешней обойме подшипника, на внутренней обойме подшипника, связаны с работой сепаратора подшипника, и с частотой вращения тел качения – шаров или роликов. Рассмотрим, для упрощения без промежуточных математических выкладок, формулы для расчета этих частот.
Частота обкатывания тел качения по внешней обойме подшипника, часто в литературе обозначаемая как BPFO:
Fн = Nтк / 2 х F1 ( 1 - Dтк / Dc х cosj )
где: Nтк - количество тел качения в одном ряду подшипника;
F1 - оборотная частота вращения ротора;
Dтк - диаметр тела качения;
Dc - средний диаметр сепаратора;
j - угол контакта тела качения с обоймой.
Частота обкатывания тел качения по внутренней обойме - BPFI:
Fв = Nтк / 2 х F1 ( 1 + Dтк / Dc х cos j )
Частота работы сепаратора - FTF:
Fс = 1 / 2 х F1 ( 1 - Dтк / Dc х cos j )
Частота работы (вращения) тел качения - BSF:
Fтк = 1 / 2 х F1 х Dтк / Dc ( 1 - Dтк2 / Dc2 х cos2 j )
Как видно из этих формул, для точного определения характерных гармоник работы подшипника качения достаточно 4 первичных параметров, три из которых являются конструктивными, а четвертый определяется рабочей частотой вращения ротора.
Данные формулы расчета характерных подшипниковых частот являются достаточно простыми, но не всегда удобными для практики. Сложность заключается в том, что они включают в себя угол контакта тел качения с обоймами. Этот параметр не всегда известен точно и в процессе работы подшипника, по мере износа рабочих поверхностей подшипника, может изменять свое значение.
В практике удобнее использовать более простые формулы, не включающие в себя этот угол, в результате, естественно, менее точные, чаще всего приемлемые для практической диагностики. Приведем и эти формулы:
Частота обкатывания тел качения по внешней (наружной) обойме - BPFO:
Fн = F1 ( Nтк / 2 - 1,2 )
Частота обкатывания тел качения по внутренней обойме - BPFI:
Fв = F1 ( Nтк /2 + 1,2 )
Частота работы сепаратора - FTF:
Fс = ( 1 / 2 - 1,2 / Nтк )
Частота вращения тел качения - BSF:
Fтк = ( Nтк / 2 - 1,2 / Nтк )
Алгоритм использования этих формул достаточно прост – если в спектре вибрационного сигнала появляются гармоники с такими частотами, то можно говорить о дефектах в соответствующем элементе подшипника. Так это можно трактовать теоретически, практически же все выглядит сложнее.
Использовать эти формулы, опираясь на анализ «прямых спектров» (классических спектров Фурье от всего сигнала) следует очень осторожно, достоверность диагностики с их использованием может быть не высокой. Достаточно часто даже при наличии в подшипнике явного дефекта в вибросигнале характерные частоты могут полностью отсутствовать, иметь сдвиг по частоте, или иметь очень малый уровень.
3.1.1.2. Методы диагностики дефектов подшипников
Для оценки технического состояния и диагностики дефектов подшипников качения разными авторами и компаниями разработано достаточно много различных методов. Естественно, что все эти методы, различные по своим теоретическим предпосылкам, имеют разную трудоемкость, требуют различного приборного обеспечения и могут применяться для различных целей. Конечно, итоговая информация, полученная в результате использования этих методов, имеет различную информативность и достоверность.
В данном разделе мы попытаемся, очень обзорно и поверхностно, рассмотреть и сравнить основные методы, чаще всего применяемые в практике. В основе сравнения будем использовать параметр, который назовем как практическая применимость и эффективность. При этом будем систематизировать эти методы исходя только из основных, базовых, теоретических предпосылок, возможности применения их на различных этапах развития дефектов подшипников.
В самом общем случае оценка технического состояния и поиск дефектов подшипников качения может производиться при четырех наиболее распространенных методов, по следующим диагностическим параметрам:
1. По величине СКЗ виброскорости
Данный метод позволяет выявлять дефекты подшипников на последних стадиях, начиная, примерно, с середины третьего этапа развития дефекта, когда общий уровень вибрации значительно вырастает. Данный метод диагностики прост, имеет нормативную базу, требует минимальных технических затрат и не требует специального обучения персонала, применяется при диагностике «массового» и сравнительно недорогого вращающегося оборудования.
2. Диагностика дефектов подшипников качения по спектрам вибрационных сигналов
Данный метод применяется на практике достаточно часто, хотя и не обладает высокой чувствительностью, но он позволяет выявлять, наряду с диагностикой подшипников, большое количество других дефектов вращающегося оборудования. Этот метод позволяет начинать диагностику дефектов подшипников примерно с середины второго этапа, когда энергия резонансных колебаний вырастет настолько, что будет заметна в общей картине частотного распределения всей мощности вибросигнала. Для реализации данного метода необходим хороший измерительный прибор достаточно высокого уровня, и специально подготовленный персонал.
3. Диагностика дефектов по соотношению пик / фон вибросигнала
Основы метода иллюстрируются рисунком 3.1.1.1. Этот метод разрабатывался несколькими компаниями и имеет много различных, примерно одинаковых по эффективности, практических модификаций. Это метод HFD (High Frequency Detection - метод обнаружения высокочастотного сигнала), метод SPM (Shock Pulse Measurement - метод измерения ударных импульсов), метод SE (Spike Energy - метод измерения энергии импульса), а также еще несколько других, но менее известных методов. Лучшие разновидности данного метода позволяет выявлять дефекты подшипников качения на достаточно ранних стадиях, начиная примерно с конца первого этапа развития. Приборы, реализующие данный метод диагностики дефектов достаточно просты и дешевы.
4. Диагностика дефектов подшипников качения по спектру огибающей вибрационного сигнала
Данный метод позволяет выявлять дефекты подшипников на самых ранних стадиях, начиная примерно с середины первого этапа. Теоретически данный метод диагностики дефектов подшипников качения может базироваться и на анализе акустических сигналов, и на анализе вибрационных сигналов. В первом случае метод называется SEE (Spectral Energy Emitted - анализ излучаемой спектральной энергии), и для своей работы использует специальный датчик акустического излучения. Чаще всего для такой диагностики используют акустические детекторы утечек различных модификаций, работающие в диапазоне частот до 100 кГц. В этом случае измерение акустических параметров производится дистанционно, с некоторого удаления от контролируемого подшипника. Если для измерения вибрационных сигналов используются «обычные контактные датчики вибрации», то применение этого метода не требует использования специального оборудования. Развитием данного метода много занимались российские диагносты, в настоящее время считается уже классическим методом для анализа вибросигналов с подшипников качения.
Все вышеперечисленные методы диагностики дефектов подшипников качения различаются не только теоретическими предпосылками, положенными в их основу. Они различаются типом используемого диагностического оборудования, его стоимостью, необходимой подготовкой персонала и конечно своей эффективностью. Практически всегда справедливо простое правило - чем на более ранней стадии, и чем более достоверно необходимо обнаруживать дефекты подшипников, тем дороже это стоит.
Кроме того всегда следует помнить и учитывать, что диагностика состояния подшипников является только частью общего диагноза по оборудованию. Полный анализ состояния оборудования обычно проводится по спектрам вибросигналов, поэтому при выборе метода диагностики подшипников качения предпочтение следует отдавать диагностике по спектрам огибающей, что делает этот метод практически универсальным. При таком подходе полный набор технических средств, предназначенный для диагностики состояния оборудования, будет минимальным по объему и стоимости.
В случае, если стандартная спектральная диагностика данного типа оборудования постоянно не проводится, то для ранней диагностики состояния подшипников качения весьма эффективно применение методов, основанных на сравнении уровней фона и пика вибросигнала. Эти методы обладают достаточной для стандартной практики работы специалистов по вибрационной диагностике достоверностью. Очень большим достоинством этих методов является то, что для своей реализации они не требуют дорогих и специализированных виброметров.
Для того, чтобы при наличии явного дефекта в подшипнике необходимо выполнение целого ряда различных требований. Эти требования обусловлены конструктивными, эксплуатационными, и методическими особенностями проведения диагностики подшипников качения различными методами.
Основное требование к конструкции подшипникового узла следующее - должен существовать хороший акустический контакт между зоной установки подшипника качения, и возможным местом установки измерительного датчика. Здесь использован термин «акустический контакт» по той причине, что большая часть интересующих нас вибрационных частот находится в зоне акустической слышимости. Конечно, более правильно было бы говорить о передаче вибрационных сигналов от контролируемого подшипника к датчику, но в данном случае это равноценно.
Измерение параметров технического состояния контролируемого подшипника должны проводиться в определенных условиях:
- Контролируемый подшипник должен быть нагружен достаточным усилием, чтобы «дефект мог проявиться» в измеряемых вибрационных сигналах. При невыполнении этого условия диагностика в режиме «on-line» становится бессмысленной.
- Дефектная зона подшипника качения должна периодически проходить через зону нагрузки подшипника.
- Желательно, чтобы в контролируемом оборудовании не было других источников вибрационных сигналов с частотой, равной частоте дефектов, или их влияние было ослаблено в зоне контроля.
Используемое для диагностики измерительное оборудование должно обладать определенными свойствами:
- Частотные параметры измерительного датчика должны охватывать весь возможный диапазон частот, которые могут возникнуть в контролируемом подшипнике, и который представляет «диагностический интерес».
- Регистратор и анализатор вибрационных сигналов, используемый для анализа «прямых спектров» подшипников качения, должен обеспечивать, после обработки, получение спектра вибросигнала с разрешением не меньше 1600 - 3200 линий.
Эти требования относятся ко всем методам диагностики подшипников качения по спектрам и спектрам огибающей, которые базируются на использовании вышеприведенных формул расчета подшипниковых частот.
В завершение данного общего раздела, касающегося общих вопросов диагностики, хочется коснуться важного методического вопроса, связанного с диагностикой «тихоходных подшипников». Такие подшипники в больших количествах используются в бумагоделательных машинах, в различных конвейерных линиях и подъемных механизмах.
Смысл
рассматриваемого вопроса достаточно прост, он заключается в том, чтобы определить,
какими частотными параметрами должны обладать измерительные приборы, предназначенные
для диагностики таких подшипников качения, и каковы особенности такой диагностики.
Например, если нужно диагностировать подшипник, частота вращения которого равна
0,2 Гц, т. е. если контролируемый подшипник делает один оборот за пять секунд,
то какими должны быть частотные свойства используемого диагностического
прибора, измерительного датчика? В каком частотном диапазоне должны
производиться измерения, чтобы полученной информации хватило для проведения
корректной диагностики подшипника.
Для ответа на этот вопрос обратимся к рисунку 3.1.1.3., на котором показан временной сигнал, зарегистрированный на дефектном подшипнике, имеющем раковину на внутренней обойме.
Приведенная на рисунке вибрационная картина понятна и наглядна. Один раз в пять секунд дефектная зона внутренней обоймы попадает в нагруженную зону подшипника, и при прохождении через дефектную зону тел качения возникают динамические удары. После каждого удара в дефектной зоне возникают свободные затухающие колебания с частотой около 2 кГц. В приведенном примере мы имеем «серии» из трех ударов, т. е. за время прохождения дефектной зоны в нее «попадают» три тела качения подшипника. Это «рафинированная» вибрационная картина реального дефекта, достаточно часто встречающегося в практике.
Вопрос стоит следующим образом, какими частотными свойствами должен обладать измерительный датчик, и в каком диапазоне частот мы должны провести измерения, чтобы, например, диагностировать дефект в данном подшипнике при помощи прямых спектров.
Для начала определимся с тем, какая зона нашего вибрационного сигнала представляет для нас интерес, от этого зависит многое. Очевидно, что если речь идет о повторяющихся импульсах, то мы должны включить в рассмотрение не менее 2-3 оборотов контролируемого ротора, а в идеале 4-5, чтобы было можно уверенно диагностировать дефекты сепаратора подшипника качения. Это связано с тем, что частота гармоники дефектного сепаратора обычно чуть меньше 0,5 Гц, т. е. такой дефект «обкатывается» один раз за два оборота ротора. Если мы включим в рассмотрение 4 оборота ротора, то получим, что мы должны зарегистрировать вибрационный сигнал, длительность которого равняется 20 секунд.
Выше мы уже говорили, что частота свободных колебаний после динамических ударов, в нашем примере, равняется 2 кГц. Чтобы корректно зарегистрировать и диагностировать эту гармонику на спектре мы должны вести регистрацию с частотой не менее 5 кГц, а лучше больше, например, хотя бы 6 кГц. Это логично вытекает из правила Найквиста.
Теперь становится понятным, что одна регистрация вибрационного сигнала на тихоходном подшипнике должна производиться с частотой 6 кГц, и длительностью 20 секунд. Итоговая длина одной выборки должна составлять не менее 120 тысяч отсчетов АЦП. Такими возможностями обладают далеко не все приборы регистрации вибрационных сигналов, в том числе самые лучшие, это специфическое требование. Для 95% процентов приборов, имеющихся на современном рынке, максимальная длина выборки сигнала не превышает 8192 отсчета.
Второй важный вопрос, а каков частотный диапазон измерительного датчика, предназначенного для диагностики тихоходных подшипников качения? Что самое парадоксальное, многие утверждают, что чем ниже этот диапазон, тем лучше. А какой же диапазон необходим для диагностики подшипника, сигнал с которого приведен на нашем рисунке? При опросе 90% специалистов сказали, что необходим датчик с нижней граничной частотой от 0,05 Гц, и даже ниже.
Когда мы акцентировали внимание на том, что основная диагностическая частота составляет 2 кГц, это есть частота свободных колебаний конструкций «вокруг подшипника» после динамических ударов в зоне дефекта, даже после этого не все изменили свои требования к частотным свойствам измерительного датчика. Еще раз подчеркнем, что все эти рассуждения справедливы только для диагностики подшипников качения, для диагностики подшипников скольжения требования другие, более стандартные.
Заключим данные рассуждение следующим. Диагностику тихоходных подшипников качения следует проводить при помощи «импульсных» методов. Диагностика с использованием «прямых» спектров практически невозможна, а с использованием спектров огибающей вибрационного сигнала весьма сомнительна.
3.1.1.3. Диагностика дефектов по общему уровню вибрации
Данный способ оценки технического состояния и диагностики дефектов в подшипниках вообще, и в подшипниках качения в частности, входит в широко распространенную простейшую практику оценки общего технического состояния вращающегося оборудования по общему уровню вибрационного сигнала. Такая диагностика производится техническим персоналом без специальной вибрационной подготовки. Для проведения такой диагностики дефектов подшипников качения вполне достаточно использования простейшего виброметра, измеряющего общий уровень вибрации.
Как уже говорилось выше, такая диагностика дефектов подшипников качения позволяет определять дефекты только на самой последней стадии их развития, когда они уже приводят или уже привели к деградации состояния подшипников, повышению общего уровня вибрации. Диагностику дефектов подшипников по величине СКЗ виброскорости, а только для такой размерности вибрационного сигнала существуют критерии технического состояния оборудования, можно интерпретировать уже как предаварийную.
Критерии технического состояния, и степени развития дефектов в данном методе полностью ориентированы на соответствующие нормативные значения уровней вибрации, принятые для данного механизма. Дефектным в этом методе диагностики считается такой подшипник качения, вибрации которого превысили общую норму для агрегата, это является признаком дефектного состояния контролируемого подшипника качения. При таком пороговом повышении значения уровня вибрации, замеренной на опорном подшипнике, обслуживающему персоналу необходимо принимать решение о возможности дальнейшей работы агрегата или об остановке оборудования и замене подшипника.
Первые признаки дефекта подшипника данным методом диагностики обнаруживаются при обследовании оборудования персоналом достаточно поздно, примерно за несколько месяцев, недель или даже дней, что зависит от целого ряда особенностей работы данного подшипника, до момента полного выхода подшипника из строя. Несмотря на такое позднее обнаружение дефектов, и несколько скептическое отношение к этому методу специалистов со стажем, такой метод диагностики состояния подшипников качения достаточно широко используется в практике и дает неплохие результаты в тех случаях.
Максимальными преимуществами метод обладает в случаях, когда:
- Основной задачей проведения диагностического обследования оборудования является только предотвращение аварий и их последствий, пусть даже диагностическая информация о наличии дефекта будет получена на достаточно позднем этапе.
- Останов оборудования для замены подшипника могут быть выполнены в любое время, без какого - либо ущерба для работы контролируемой установки и технологического цикла всего предприятия, без нарушения общего процесса.
- Если цикличность проведения ремонтных работ на контролируемом оборудовании такова, что оставшийся срок службы подшипника с диагностированным дефектом, пусть даже минимальный, всегда превышает оставшееся время работы до его вывода в ремонт по другим причинам.
Достоинством такого, самого простейшего метода диагностики дефектов подшипников качения по общему уровню вибрации, является так же и то, что для его применения не требуется практически никакого дополнительного обучения обслуживающего, а часто и эксплуатационного персонала. Кроме того стоимость технического оборудования, необходимого для данного метода диагностики, минимальна.
Если на предприятии ранее не велись какие-либо работы по вибрационной диагностике, то данный метод диагностики обеспечивает наибольшую эффективность при своем внедрении. Применение всех других методов диагностики подшипников качения всегда требует больших начальных материальных затрат, и дает экономический эффект только на более поздних стадиях работы.
В заключении по данному вопросу следует сказать, что неожиданно высокую эффективность может иметь диагностика дефектов подшипников качения наиболее простым способом – «на слух». Для этого необходимо наличие какого-либо устройства для прослушивания подшипников, например типа стетоскопа, или виброметра с подключаемыми наушниками. Если ничего даже этого нет, то можно воспользоваться любой сухой деревянной палочкой достаточных размеров.
Если приложить ее одним концом к контролируемому подшипнику, а вторым концом к уху, то при наличии дефекта в подшипнике можно очень явственно услышать высокий, негромкий, приятный звон, называемый иногда «бронзовыми колокольчиками». Стоит только один раз его услышать, и спутать его уже будет нельзя ни с чем. Достоверность диагностики дефектных подшипников таким методом очень велика.
3.1.1.4. Диагностика дефектов подшипников по спектрам сигналов
Большинство специалистов по вибрационной диагностике, если они начинают заниматься подшипниками качения, ожидают наибольшей достоверности и наибольшего эффекта при внедрении диагностики по классическим спектрам вибрационных сигналов. Такие спектры, в отличие от спектров огибающей вибрационного сигнала, также используемых для диагностики подшипников качения, достаточно часто называют «прямыми», и этот термин мы тоже будем применять.
К сожалению, чаще всего именно здесь их оптимистическим ожиданиям не суждено будет сбыться. Мало того, что сама процедура диагностики является достаточно сложной и противоречивой, достоверность большинства практических диагнозов по состоянию подшипников качения, полученных при использовании таких «прямых» спектров вибрационных сигналов, является неожиданно низкой. Метод, предназначенный для решения самых сложных диагностических задач вращающегося оборудования, не дает хороших результатов при диагностике «копеечных» подшипников качения!
«Неожиданность» такого парадокса запрограммирована заранее и заложена в особенностях диагностики по спектрам вибрационных сигналов. Ошибки диагнозов заранее прогнозируемы и заключаются в том, что классический спектр есть, по своему определению, распределение мощности исходного временного вибросигнала в частотной области. По этой, причине появление на спектре характерных гармоник того или иного элемента подшипника качения, следует ожидать только в том случае, когда дефект разовьется до такой степени, когда мощность его гармоник будет соизмерима с мощностью «механических» гармоник, связанных с небалансом, расцентровкой. Только в этом случае на спектре можно уверенно диагностировать «подшипниковые» гармоники, когда они будут иметь не только большую амплитуду, но и существенную мощность.
Для того, чтобы повысить чувствительность данного диагностического метода к «подшипниковым гармоникам» с малой мощностью, применяются различные способы, например, амплитуды гармоник в анализируемых спектрах представляются в логарифмическом масштабе. Это конечно помогает, но до определенного значения, когда гармоники уже начинают маскироваться общим «белым шумом», который в вибрационных сигналах имеет значительную амплитуду.
В соответствии с приведенной в начале главы градацией развития дефектов подшипников качения на этапы можно сказать, что диагностика по спектрам вибрационных сигналов может уверенно выявлять дефекты подшипников качения, начиная только с конца первого этапа их развития, а чаще с середины второй зоны. Причем даже на этом уровне диагностика по «прямым» спектрам вибрационных сигналов является делом достаточно непростым, и имеет ряд специфических особенностей.
Ниже мы попытаемся рассмотреть эти особенности, значительно усложняющие диагностику дефектов подшипников качения по прямым спектрам.
Начнем с требований, которые предъявляются к приборам регистрации и анализа вибрационных сигналов. Используемый для диагностики подшипников качения измерительный прибор должен обязательно иметь высокое частотное разрешение, не менее, чем 3200 линий в спектре. В противном случае произойдет «размазывание» мощности узкого ударного пика дефекта по достаточно широкой спектральной полосе, что приведет к резкому занижению амплитуды характерной подшипниковой гармоники, что однозначно исказит результаты проводимой диагностики. Как мы уже писали раньше, таких приборов находится в эксплуатации не так много, обычно частотное разрешение приборов значительно меньше.
Вполне понятно, что раз диагностика подшипников качения, чаще всего, ведется на анализе динамических процессов, то измерения необходимо вести в размерности виброускорения, в котором эти процессы более значимы. Хотя в некоторых методах диагностики необходимо анализировать энергетическую составляющую колебаний, для чего следует пользоваться измерениями в размерности виброскорости.
Далее обратимся к основным особенностям проявления дефектов подшипников в исходных вибрационных сигналах, и в получаемых на их основе «прямых» спектрах мощности. Таких характерных особенностей существует несколько.
- Во-первых, это наличие на зарегистрированном сигнале вибрации явно выраженных периодических ударных процессов. Каждый удар, возникающий при обкатывании зоны дефекта телами качения подшипника, характеризуется целым набором параметров - максимальной амплитудой удара, частотой возникающих свободных колебаний, и скоростью затухания этих колебаний.
- Во-вторых, это наличие в спектре вибрационного сигнала большого количества «нецелых» компонент, или, беря за базу оборотную частоту поддерживаемого ротора, гармоник с дробными номерами. Частоты этих нецелых гармоник определяются подшипниковыми соотношениями. Кроме того, при определенных типах дефектов подшипников эти гармоники сами создают свои семейства и гармоники на частотах взаимного биения, которые еще больше усложняют процедуру диагностики.
- В-третьих, это наличие в спектре вибрационного сигнала широкополосных «поднятий», своеобразных энергетических горбов вблизи подшипниковых частот, и частот собственных резонансов элементов механической конструкции. Идентифицировать причину возникновения этих горбов на спектре, а также связать их параметры с первичными дефектами подшипников качения очень сложно.
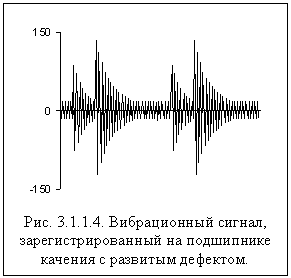
Рассмотрим сначала форму ударных импульсов, возникающих при ударных воздействиях от дефектов подшипников, возникающих в вибрационном сигнале. Для этого рассмотрим простейший пример вибрационного сигнала, приведенный на рисунке 3.1.1.4., зарегистрированного на дефектном подшипнике качения. После каждого удара в дефектной зоне подшипника возникают свободные резонансные колебания, которые обычно затухают по экспоненциальному закону.
Вероятность появления таких ударных периодических импульсов, имеющих весьма характерный вид, сопровождающих процесс обкатывания дефекта подшипника, близка к 100 %. Для описания формы этих процессов особенностей даже придуман специальный термин – «золотая рыбка». Наличие импульсов такой формы в вибрационном сигнале является надежным диагностическим признаком для выявления дефектов подшипников.
Частота следования этих «золотых рыбок», точнее говоря их плавников и хвостиков, во временном сигнале должна достаточно точно соответствовать частоте, характеризующей дефект того или иного элемента подшипника. Интенсивность «золотых рыбок», степень их выраженности, превышения над общим фоном вибрации, зависит от степени развития дефекта. Пример такого вибросигнала с двумя «золотыми рыбками» приведен на нашем рисунке. Сразу же обратим внимание читателя на то, что «на один оборот ротора» может приходиться различное количество ударных импульсов, частота их следования определяется не оборотной частотой ротора, а расчетными «подшипниковыми» частотами.
В реальных вибрационных сигналах «золотая рыбка» не бывает такой красивой, чаще всего форма ее является более «лохматой». У нее имеются различные «дополнительные плавники», располагаемые сверху, или снизу. Ударные импульсы могут следовать один за другим, часто даже наслаиваясь друг на друга. Все это зависит от реальной частоты следования ударов от дефектов, и от собственных резонансных свойств механической конструкции или ее отдельных элементов.
Вторая, основная диагностическая особенность заключается в наличии специфического проявлении дефектов подшипников качения в «прямых» спектрах вибрационных сигналов. Непосредственно при проведении диагностики можно выявить три типа возможных, наиболее часто встречающихся типа спектров вибросигналов, соответствующих различным этапам развития дефектов.
Диагностическая стадия 1
Первые признаки дефектов на спектре вибросигналов появляются тогда, когда дефект подшипника, возникнув, разовьется до такого уровня, что выделяемая им энергия (в золотых рыбках) станет сравнительно заметной в общей энергии вибрации подшипника, т. е. будет представлена на спектре. Применительно к вышеописанному разделению на этапы развития дефектов, приведенному на рисунке 3.1.1.1., это примерно конец первого этапа - начало второго. По срокам это бывает примерно несколько месяцев с момента начала развития дефекта. Пример спектра первой стадии приведен на рис. 3.1.1.5.
В
этом спектре, наряду с первыми, механическими, гармониками оборотной частоты
вращения ротора, появляется пик на характерной частоте дефекта того или иного
элемента подшипника. На этой стадии развития дефекта характерная «подшипниковая»
гармоника уже хорошо видна на спектре, что позволяет достаточно точно выявлять
дефектный элемент, особенно если представлять амплитуду гармоник в логарифмическом
масштабе.
По своей амплитуде пик характерной гармоники уже соизмерим с амплитудой первой или второй гармоник оборотной частоты ротора, но по своей мощности еще много уступает им. На спектре это выражается тем, что пик подшипниковой гармоники является очень узким. Дефект появился, но еще не является сильно развитым, динамические удары при обкатывании дефекта есть, но амплитуда и энергия их еще не очень значительна.
Эта
стадия, соответствующая специфическому проявлению дефектов подшипников в
спектрах вибрационных сигналов, и завершается тогда, когда амплитуда
характерной гармоники достигает своего максимума, примерно равного амплитуде
оборотной гармоники, и уже больше не растет. Она если и будет превышать
оборотную гармонику, то не на много, не более 30%. Причина этого проста –
энергия подшипниковых гармоник автоматически «вносится» преобразованием Фурье - FFT в состав оборотной гармоники. Как
следствие срабатывает логическое правило, говорящее о том, что одно слагаемое
не может быть больше итоговой суммы.
Диагностическая стадия 2
Следующая стадия развития дефекта подшипника качения начинается тогда, когда на спектре рядом с подшипниковой гармоникой, очень близко, появляется первая пара боковых гармоник, располагающихся слева и справа.
Появление боковых гармоник обозначает, что начался этап пространственного расширения зоны дефекта в подшипнике вдоль поверхностей качения, что иллюстрируется рисунком 3.1.1.6. В этой зоне дефект имеет уже такие размеры (глубину), что при «проваливании» тела качения в зону дефекта он смещается настолько, что основную нагрузку по поддержке вала механизма уже берут на себя рядом расположенные тела качения. «Ступенька», с которой «прыгает» тело качения в зоне дефекта, практически не может быть очень большой, ее величина зависит от общей степени износа подшипника качения. В результате увеличение амплитуды динамических импульсов больше не происходит. Вся энергия этих импульсов теперь уходит не на углубление, а уже на расширение зоны дефекта, возникающее за счет постепенного «раскрашивания» границ зоны дефекта.
На этой стадии диагностики дефектов подшипников по спектрам вибрационных сигналов значительно увеличивается «вклад дефекта» в общую вибрацию контролируемого механизма. Подшипниковая гармоника увеличивает свою мощность до такого значения, что становится соизмерима с основными механическими гармониками - первой и второй. Результатом наличия в вибросигнале двух, как минимум, гармоник - синхронной и несинхронной примерно одинаковой мощности возбуждает в агрегате частоты биений. Эти частоты биений проявляются в спектре в виде боковых полос вблизи характерной подшипниковой гармоники. По мере роста мощности подшипниковой гармоники с расширением зоны дефекта число боковых полос и их мощность постепенно возрастает.
Дальнейшее развитие дефекта приводит уже к появлению новых семейств гармоник,, уже от самой характерной подшипниковой частоты. Обычно появляются гармоники с номером два и три от основной частоты подшипникового дефекта. Рядом с каждой такой гармоникой слева и справа тоже будут иметь место боковые частоты, число пар которых может быть достаточно большим. Чем более развит дефект, тем больше боковых гармоник и у гармоник частоты дефекта.
Гармоники от подшипниковых частот с большим номером, чем три, регистрируются достаточно редко. Это происходит по той причине, что хотя более высокочастотные гармоники и возникают, но мы не можем их зарегистрировать на внешней поверхности подшипниковых опор. Чем выше частота возникающих колебаний, тем более интенсивно это колебание будет затухать внутри подшипниковой опоры, на участке от места возникновения до места установки первичного измерительного датчика.
Пример
спектра вибросигнала подшипника качения с таким уровнем развития дефекта показан
на рисунке 3.1.1.7. На этом спектре есть две гармоники от характерной частоты
подшипникового дефекта, первая и вторая. Вокруг каждой гармоники расположено по
две пары боковых гармоник, расположенных слева и справа.
Износ подшипника, обладающего таким набором характерных гармоник в спектре, уже очевиден. Пространственно он может простираться почти по всей рабочей поверхности подшипника, он уже стал групповым, захватив несколько элементов подшипника. Подшипник нуждается в замене или к такой процедуре нужно интенсивно готовиться.
Хочется завершить описание этого этапа развития дефекта в подшипнике качения небольшим, но методически важным сравнением, связанным с использованием общего подхода к диагностике дефектов вращающегося оборудования. При внимательном рассмотрении видно, что такой состав гармоник подшипниковой частоты, который показан на рисунке 3.1.1.7., если не брать во внимание боковые гармоники, очень похож на состав гармоник оборотной частоты ротора, имеющий место при наличии механического ослабления в роторе, так же называемого люфтом, описанном в соответствующем разделе.
Такое совпадение типов дефектов реально есть и на самом деле. Появление на спектре гармоник подшипниковой частоты говорит именно о развитии механического ослабления, так как при такой степени развития дефекта фиксация ротора в дефектном подшипнике становится уже недостаточно точной. Следствием такого совпадения проявления дефектов является примерное равенство наборов основных гармоник, возникающих в обоих случаях – при общем ослаблении ротора, и при ослаблении в опорном подшипнике.
Диагностическая стадия 3
Это последняя стадия развития дефектов подшипника. В конце этой стадии подшипник уже полностью деградировал и перестал исполнять свои прямые функции - обеспечивать вращение валов при минимальных затратах на трение. Потери на трение в подшипнике велики, и вращение ротора затруднено.
Развитие дефекта подшипника на этой стадии, при диагностике его по спектрам вибрационных сигналов, проходит следующим образом. Износ подшипника достигает такой стадии, когда характерная частота дефекта, из-за очень большого расширения зоны дефекта, становится нестабильной, такая же участь постигает боковые гармоники. Наложение многих семейств гармоник, каждое из которых состоит из основной частоты и боковых гармоник, создает достаточно сложную картину. Если в этих семействах основные гармоники различаются по частоте немного, то сумма всех этих частот представляет собой общее поднятие спектра, «энергетический горб», захватывающий такой диапазон частот, куда входят все гармоники всех семейств от всех уже существующих дефектов подшипника качения.
На общем фоне «энергетического горба» могут выделяться отдельные гармоники, но обычно все они носят случайный характер, как по частоте, так и по амплитуде, и уже практически ничего конкретного не отражают. Они просто увеличивают мощность, сосредоточенную в этом частотном диапазоне спектра.
Практически
вся мощность вибрационного сигнала сосредоточена не в зоне наиболее значимых механических
гармоник, с первой по десятую, а в зоне характерных гармоник, соответствующих
имеющим место дефектам диагностируемого подшипника качения. Правда на этом
этапе таких дефектов уже много, и это понятно, подшипника уже практически нет,
есть «сплошной дефект» всех элементов подшипника. Для иллюстрации этой стадии
на рисунке 3.1.1.8. приведен спектр вибросигнала. На рисунке достаточно хорошо
видны все вышеперечисленные особенности диагностирования третьей стадии развития
дефекта.
Кроме того в диапазоне гармоник, свойственных механическому ослаблению и увеличенному зазору в подшипнике поднимается лес целых гармоник оборотной частоты. Все они по своим параметрам соответствуют вышеназванным механическим причинам. Причины возникновения таких гармоник вполне понятна, в контролируемом подшипнике велики все зазоры, о чем мы уже писали немного раньше. Только на этом этапе мы имеем механическое ослабление не на уровне дефектов тел качения, а на уровне увеличения зазоров в опорных подшипниках. В результате и возникают множественные гармоники оборотной частоты ротора.
Диагностическое заключение о техническом состоянии такого подшипника качения очень простое - он нуждается в скорейшей замене, т. к. возможность возникновения аварийной ситуации с контролируемым оборудованием очень велика.
Здесь мы подошли к самому главному в диагностике любого оборудования любым методом. Каковы финальные и промежуточные критерии для оценки технического состояния подшипника качения? Как оценить уровень развития выявленного дефекта - на основании сравнении амплитуд конкретных гармоник, или анализируя иные параметры гармоник характерных подшипниковых частот. К сожалению, в очередной раз вынуждены разочаровывать нашего читателя, таких однозначных для практики значений нет, или, если говорить еще более точно, нам они неизвестны.
В практике диагностам чаще всего приходится оперировать терминами типа «больше – меньше», или «более развитый дефект – менее развитый». Все зависит от очень многих параметров – от типа подшипника, особенностей его монтажа, величины технологической нагрузки на подшипник, и от много другого. Говоря иными словами, уровень дефекта подшипника в каждом механизме свой, уникальный. На величину порога каждого дефекта даже сказывается выбранное место для установки датчика, удаление от места возникновения дефекта. Например, в самом простейшем случае, дефект внутренней обоймы подшипника качения менее заметен в вибрационном сигнале, чем дефект его внешней обоймы.
Определение истинного уровня недопустимого развития дефекта подшипников качения, точнее говоря определение истинной степени развития каждого дефекта каждого подшипника, чаще всего представляет наибольшую сложность, и значительно увеличивает трудоемкость использования метода диагностики по прямым спектрам. Нет ничего полезнее и важнее, чем практический опыт, накопленный по результатам диагностических измерений и сравнения их с результатами, полученными в процессе ремонтных работ.
В заключение по данному вопросу хотелось бы немного повторить уже сказанное, дополнив его некоторыми специфическими признаками:
- Все подшипниковые частоты обычно модулируются частотой вращения ротора, что приводит к возникновению вокруг них характерных боковых гармоник. По мере углубления дефекта число боковых гармоник растет. Дополнительная мощность вибрации от дефекта оказывается сосредоточенной не в основной гармонике дефекта, а вокруг нее, причем в достаточно широком диапазоне частот.
- Достаточно часто бывает, что реальные частоты характерных гармоник от отдельных элементов подшипника не соответствуют рассчитанным значениям, причем по мере «углубления и расширения зоны дефектов» это отличие может увеличиваться.
- Чаще всего при значительных степенях развития дефектов на спектре возникают «энергетические горбы» - участки с общим поднятием уровня, имеющие большое количество случайных пиков. Такие «горбы» могут возникнуть как вблизи характерной частоты, так и вблизи частоты резонанса конструкции или ее отдельного элемента. Часто «энергетический горб» бывает в двух местах спектра, и на характерной частоте и на резонансной. Достаточно часто, при развитом дефекте, сама гармоника характерной частоты, вокруг которой появился и вырос «энергетический горб», на спектре отсутствует. Иногда число «горбов» может быть три или даже больше.
3.1.1.5. Диагностика с использованием пик - фактора
В данном разделе кратко рассмотрим те методы диагностики подшипников качения, в которых идет анализ наличия дефектов подшипников по соотношению на временных вибросигналах пиков и общего уровня «фона» вибрации. Одна из таких временных зависимостей, по которым может выполниться такая диагностика, приведена в начале данного раздела на рисунке 3.1.1.1.
В силу устоявшейся практической привычки мы называем эти, во многом достаточно разные методы диагностики подшипников качения, общим наименованием – «диагностикой по пик – фактору», хотя разработчики многих компаний придумали разновидностям этого метода иные названия. Применяемый нами диагностический признак «пик – фактор» не является единственным и полностью общепринятым в практике, но в силу того, что оно хорошо отражает физический смысл этого метода, мы используем его преимущественно.
Как уже говорилось выше, этот метод диагностики подшипников качения имеет несколько достаточно широко известных разновидностей. Эти разновидности разрабатывались разными компаниями, в них несколько по-разному производят сравнение уровней пика и фона вибросигнала. В одном методе для сравнения берется амплитуда пика, в другом энергия, фоновый уровень также может рассчитываться по-разному.
Мы уже называли основные разновидности этого метода:
- Диагностика с использованием СКЗ вибрационного сигнала и пиковых значений – классический метод диагностики по пик фактору.
- Диагностика с использованием соотношения эксцесса вибрационного сигнала и общего уровня.
- Метод HFD (High Frequency Detection - метод обнаружения высокочастотного сигнала).
- Метод SPM (Shock Pulse Measurement - метод измерения ударных импульсов).
- Метод SE (Spike Energy - метод измерения энергии импульса).
Лучшие разновидности данного метода позволяет выявлять дефекты подшипников качения на достаточно ранних стадиях, начиная примерно с конца первого этапа развития. Приборы, реализующие данный метод диагностики дефектов достаточно просты и дешевы.
При более общем взгляде на все эти методы видно, что они, в силу одинакового теоретического, методического и даже приборного подхода к решению проблемы, имеют примерно и одинаковую трудоемкость, и почти одинаковую достоверность поставленных диагнозов. Для этих методов нужна примерно одинаковая техническая база - специализированные переносные виброметры с встроенными двумя типами детекторов вибросигналов - детектором среднего уровня вибросигнала и пиковым детектором.
Использование обобщенного количественного соотношения двух величин по типу – «средний уровень – пик» позволяет диагносту определять дефекты подшипника на достаточно ранних стадиях их развития, что является несомненным достоинством применения такого подхода к диагностике.
Каждая из известных нам компаний-разработчиков диагностических методов по своему, с использованием собственного опыта, решила проблему нормирования этапов развития диагностируемых дефектов, но практическое представление этих наработок примерно одинаково - это специальные таблицы или номограммы, достаточно удобные для практического использования. Какого - либо обобщающего исследования, сравнивающего эти методы между собой нет, да и очевидно быть не может. Все они примерно с равным успехом применяются в практике.
Вопросы методики практического проведения замеров вибрации в этих методах не имеют достаточно подробного описания. Это является результатом того, что эти достаточно простые методы диагностики ориентированы на использование персоналом, не обладающим специальной диагностической подготовкой. Поэтому сама технология проведения замеров должна быть очень простой, не «затуманенной» сложными теоретическими выкладками.
Мы не будем заниматься сравнением всех этих методов диагностики подшипников качения по «пик – фактору» между собой, не будем выискивать достоинства и недостатки как самих методов, так и компаний-разработчиков. Это уже специальный, можно даже сказать коммерческий вопрос, выходящий за пределы основных задач, решаемых данным методическим руководством.
Будет лучше, когда каждый конкретный пользователь сам примет свое решение по данному вопросу, какой из методов диагностики подшипников качения с использованием «пик – фактора» ему нравится больше всего, и с успехом использует его на практике. Тем более, такой диагностикой чаще всего занимаются не специалисты, которые, как мы надеемся, читают эту книгу.
3.1.1.6. Диагностика дефектов подшипников по спектрам огибающей
Метод диагностики состояния вращающегося оборудования при помощи спектров огибающей вибрационного сигнала получил максимальное прикладное развитие благодаря его применению именно для ранней диагностики технического состояния подшипников качения. Основы метода диагностики дефектов подшипника качения по спектру огибающей и особенности его практического применения достаточно подробно описаны выше, и поэтому не будем здесь все это повторять.
Если говорить кратко и очень просто, суть этого метода заключается в детектировании высокочастотных хвостиков «золотых рыбок» (смотри рисунок 3.1.1.4), и получения спектра от полученной огибающей высокочастотного сигнала. Полученная кривая, огибающая исходный вибрационный сигнал, является более информативной для диагностики дефектов подшипников качения, чем исходный сигнал, так как она принудительно «избавлена» от ненужной высокочастотной информации. По этой причине на спектре от данной кривой более явно представляются гармоники, соответствующие характерным подшипниковым частотам, математические формулы, предназначенные для расчета которых также приведены выше, в начале данного раздела.
Процедура проведения регистрации огибающей вибрационного сигнала достаточно сложна. Она должна учитывать несколько специфических особенностей, позволяющих повысить чувствительность метода.
- Во-первых, регистрация производится не во всем частотном диапазоне, в котором может работать измерительный прибор, а только в узкой его полосе. Поскольку первые применения данного метода чаще всего проходили с использованием аппаратуры компании «Брюль & Къер», которая наряду с созданием приборов вибрационного контроля занималась акустическими измерениями, для определения параметров полос частот использовались октавные определения. В настоящее время стандартом для расчета огибающей сигнала считается использование треть октавных фильтров, или близких к ним.
- Во-вторых, достаточно сложным является выбор необходимой полосы частот, перестройка которой осуществляется при помощи управляемых фильтров высокого порядка. С одной стороны, в этой полосе частот должны быть максимальны высокочастотные колебания, которые возникают после динамических ударов в зоне дефекта подшипника. С другой стороны, в выбранной полосе частот должны быть минимальны колебания, связанные с другими причинами, приводящими к увеличенным вибрациям в зоне опорных подшипников.
Как вы уже догадались, практически для каждого контролируемого подшипника этот вопрос приходится решать отдельно. Слишком от многих конструктивных и эксплуатационных параметров это зависит.
Мы достаточно подробно описываем этот вопрос потому, что от правильного его решения во многом зависит точность и достоверность проводимой диагностики дефектов подшипников качения.
Далее мы приведем, причем уже в конечном виде, общей таблицей, практически полный перечень дефектов, которые можно диагностировать в подшипниках качения при помощи спектральных методов - по классическим спектрам и спектрам огибающей. Всего в этой таблице приведено 15 наиболее часто встречающихся причин повышенной вибрации - дефектов подшипников с различной локализацией.
Все дефекты в таблице представлены в определенном хронологическом порядке, связанным с этапами «жизненного цикла» подшипника качения в оборудовании. Сначала идут дефекты, связанные с монтажом подшипников, с которыми приходится встречаться уже на этапе ввода оборудования в эксплуатацию. Далее идут дефекты смазки, т. е. эксплуатации подшипников. За ними следуют проблемы, связанные уже с износом рабочих поверхностей подшипников. Замыкают таблицу явно выраженные и уже сильно развитые дефекты элементов подшипников типа, «скол» и «раковина» на поверхностях качения.
В графе «тип сигнала» указывается параметр, при помощи которого наиболее эффективно проводить диагностику каждого дефекта. Это может «прямой» спектр, спектр огибающей сигнала, или их комбинация. В графе «основная частота» указывается или оборотная гармоника, или подшипниковые гармоники, являющиеся основными при диагностике. В следующей графе указывается, на какие гармоники от основной частоты следует обращать основное внимание. И в последней графе «порог» указывается уровень модуляции вибрационного сигнала основной диагностической гармоникой. Этот параметр рассчитывается по стандартным формулам обработки сигналов, которые следует взять из теории анализа модулированных радиосигналов.
N | Дефект подшипника | Тип сигнала | Основная частота | Гармоники | Порог |
1. Проблемы монтажа подшипников качения | |||||
1 | Перекос наружного кольца при посадке | Спектр + огибающая | 2 х Fн | k=1,2 | 16 % |
2 | Неоднородный радиальный натяг | Спектр + огибающая | k x F1 | k=1,2 | 13 % |
3 | Проскальзывание в посадочном месте | Огибающая | k x F1 | k=1,2,3 | 9 % |
4 | Ослабление крепления подшипника | Спектр | k x F1 | k=0.5,1,2,3 | 13 % |
5 | Задевания подшипнике и уплотнениях | Спектр | k x F1 | k=0.5,1,1.5, 2,2.5,3 | 13 % |
6 | Обкатывание наружного кольца | Спектр + огибающая | F1 | 16 % | |
2. Проблемы смазки | |||||
7 | Проблемы смазки | Фон вибрации | - | - | 20 dB |
3. Проблемы износа подшипников качения | |||||
8 | Увеличенные зазоры в подшипнике | Спектр | k x F1 | k=1,2,3,4,5,6... | 13 % |
9 | Износ поверхности наружного кольца | Огибающая | Fн | - | 16 % |
10 | Износ поверхности тел качения | Огибающая | Fc или F1-Fс | k=1,2,3 | 15 % |
11 | Износ поверхности внутреннего кольца | Огибающая | kxF1 | k=1,2,..6 | 13 % |
12 | Дефект группы поверхностей трения | Огибающая | Fн + Fв Fн+F1 | k=1,2,... | 16 % |
4. Критические дефекты подшипников качения | |||||
13 | Раковины (сколы) на наружном кольце | Огибающая | k x Fн | k=1,2,3 | 16 % |
14 | Раковины (сколы) на внутреннем кольце | Огибающая | k x Fв | k=1,2,3 | 15 % |
15 | Раковины (сколы) на телах качения | Огибающая | k x Fтк | k=1,2,3 | 15 % |
Проблемы изготовления и монтажа подшипников можно отнести к нулевому этапу развития дефектов подшипников, когда эксплуатация подшипника еще даже не началась. Проблемы смазки и начальные этапы износа соответствуют первому этапу, когда дефекты поверхностей качения только зарождаются.
Сильный
износ и зона углубления физических дефектов подшипников относятся ко второму
этапу развития дефектов в подшипниках. Как уже говорилось выше, третий этап
развития дефектов в подшипниках, начало их деградация, диагностируется уже
любым методом.
Для иллюстрации возможностей диагностики дефектов подшипников качения, приведем несколько характерных спектров огибающей вибросигнала, свойственных нескольким наиболее характерным дефектам.
На рисунке 3.1.1.9. приведен спектр огибающей вибрационного сигнала с подшипника качения, имеющего значительную раковину на наружном кольце. На приведенном спектре может иметься достаточно много гармоник, иногда даже более десяти. Все они, по своей частоте, кратны частоте обкатывания наружного кольца подшипника качения, т. е. являются ее гармониками. Других, значительных, характерных гармоник на данном спектре просто нет, поэтому вибрационная диагностика данного дефекта подшипников качения не вызывает значительных трудностей, диагностическая картина дефекта здесь достаточно простая.
На
следующем спектре огибающей вибрационного сигнала, приведенном на рисунке 3.1.1.10.,
следует диагностировать дефект типа раковина на внутреннем кольце. Здесь также
имеются гармоники характерной частоты - частоты внутреннего кольца, но здесь
есть существенное отличие. Характерные гармоники имеют боковые полосы,
сдвинутые на частоту вращения ротора. Появление боковых полос объяснялось выше
с физической точки зрения.
Можно привести еще одно объяснение причин появления боковых гармоник, с другой точки зрения. Дефект на внутреннем кольце не постоянно находится в нагруженной зоне подшипника. В течении одного оборота ротора он то находится в нагруженной зоне, то выходит из нее. Таким образом, дефект внутреннего кольца модулируется частотой вращения ротора. При внимательном рассмотрении спектра на рис. 3.1.1.10. возникает впечатление, что дефект модулируется синусоидой, по которой и располагаются амплитуды основных и боковых гармоник. Данный дефект диагностируется тоже достаточно просто.
Мы не будем приводить примеров спектров огибающих для других дефектов подшипников качения. Все они достаточно просты и могут быть легко дифференцированы после небольших рассуждений. Вся сложность проведения диагностики дефектов по спектру огибающей заключается в получении этих спектров, а дальше все уже достаточно просто.
Уровень дефекта на диагностических спектрах огибающей определяется по величине модуляции огибающей данного вибросигнала характерной гармоникой. Диагностируемые дефекты принято характеризовать в данном методе диагностики уровнями - слабый, средний и сильный. Нормированию подлежит порог сильного дефекта, в долях от которого в дальнейшем рассчитываются пороги среднего и слабого уровней. Порог среднего уровня дефекта чаще всего считают равным половине от величины порога сильного дефекта. Порог слабого уровня дефекта обычно определяют в 20 процентов от уровня порога сильного дефекта.
Самым ответственным считается корректное определение уровня порога сильного дефекта. При этом приходиться учитывать три аспекта работы подшипника и способа проведения замера вибрации:
- Чем больше размер подшипника, тем более высоким должен быть уровень порога сильного дефекта. Большой подшипник «звенит» сильнее.
- Чем выше рабочая частота вращения ротора механизма, тем выше должен быть уровень порога сильного дефекта. При быстром вращении от подшипника больше шума.
- Измерительный датчик должен располагаться как можно ближе к контролируемому подшипнику. При удалении датчика часть полезной информации затухает в конструкции и уровень порога сильного дефекта необходимо понижать.
Для каждого нового конкретного типа оборудования, точнее говоря, даже для каждого подшипника в каждом оборудовании, уровень порога сильного дефекта реально приходиться каждый раз подбирать сугубо индивидуально, не рассчитывать, а именно подбирать.
Величина порога сильного дефекта во многом зависит от удаленности элемента с дефектом от измерительного датчика. Пороги дефектов внутреннего кольца подшипника всегда ниже порогов дефектов наружного кольца. Это объясняется увеличением затухания полезной составляющей вибросигнала на более длинном пути передачи, включая дополнительные зазоры в подшипнике.
Для справки напомним, что для примера усредненные, наиболее часто встречающиеся, значения уровней порогов сильных дефектов приведены выше в таблице, где перечислены диагностируемые в подшипниках качения дефекты. В зависимости от примененного способа диагностики дефектов подшипника в таблице имеется две разновидности единиц, в которых нормируется уровень сильного порога.
При использовании для диагностики дефекта подшипника классических спектров вибросигналов уровень порога сильного дефекта может быть задан в долях от нормированного допустимого значения виброскорости на данном подшипнике или так же в процентах модуляции. При сравнении с нормой необходимо использовать не полное, абсолютное значение виброскорости на данном подшипнике, а только ту ее часть, которая наведена диагностируемым дефектом. Это несколько сложнее, но в конечном итоге более точно.
При определении качества смазки за базу для сравнения берется общий уровень «фоновой» вибрации исправного подшипника с хорошей смазкой. При повышении общего уровня «фона» вибрации в десять раз, т. е. на 20 dB, качество смазки считается неудовлетворительным.
Еще раз хочется напомнить, что в таблице приведены только общие, усредненные значения уровней порогов сильных дефектов. У конкретных подшипников возможен разброс этих значений на ± 40 % или даже несколько больше. Все зависит от типа подшипника и условий его работы.
Сам факт диагностирования того или иного дефекта подшипника несет в себе полезную информацию, но эта информация мало применима для практики. Обслуживающий персонал больше интересует вопрос о возможности дальнейшей практической эксплуатации оборудования с дефектным подшипником и тех ограничениях, которые накладывает обнаруженный дефект на возможности использования оборудования. Очень важным для практики является вопрос о сроках проведения очередного ремонта. Все эти вопросы относятся уже к сфере, относящейся к системе обслуживания оборудования.
Вопрос прогнозирования остаточного ресурса подшипника качения во многом напоминает прогнозирование общего остаточного ресурса оборудования, но и имеет свои индивидуальные особенности. Не вдаваясь в подробности, рассмотрим основные проблемы, возникающие при расчете остаточных ресурсов подшипников.
Это:
- Каждый подшипник имеет свои уникальные физические особенности, приводящие к специфическим внутренним процессам. Поэтому каждый подшипник должен описываться своей математической моделью.
- Каждый подшипник должен описываться двумя различными моделями - одна должна описывать общие процессы износа подшипника без дефектов, а другая должна описывать процессы развития внутренних дефектов.
- Время полного развития дефектов, находящихся на разных элементах подшипника, например не внешнем кольце или на сепараторе, различно. Для дефектов каждого элемента подшипника должна существовать своя математическая модель.
Даже из этого простого перечисления особенностей математического описания физических процессов в подшипнике качения видно, насколько сложна задача прогнозирования остаточного ресурса подшипника по итогам проведения вибрационной диагностики.
Первоначально состояние подшипника «контролируется» при помощи достаточно стабильной модели нормального износа, когда в нем отсутствуют внутренние дефекты. Так продолжается до момента выявления в подшипнике какого-либо дефекта. Здесь приходится отказываться от нормальной модели и переходить к моделям развития дефектов. Очень важной задачей, решаемой при переходе от нормальной модели к контролю состояния по модели развития дефекта, является как можно более точное определение времени зарождения дефекта. Чем точнее оно будет определено, тем более достоверными будут дальнейшие прогнозы по величине остаточного ресурса подшипника.
Максимальная скорость развития разных дефектов различна, поэтому контролировать следует развитие всех возможных дефектов, даже когда один из них только что зародился, а другой уже достаточно развит. Никогда нельзя заранее сказать, какой из дефектов раньше всех разовьется до недопустимого уровня и послужит причиной смены подшипника качения при ремонте.
Периодичность проведения диагностических измерений вибрации зависит от максимальной скорости развития дефекта подшипника в данном оборудовании. В практических случаях замеры могут проводиться через интервал времени от нескольких часов до одного года. При нормальной эксплуатации типового оборудования и проведении замеров примерно через шесть месяцев удается выявить большую часть дефектов на достаточно ранней стадии и предупредить аварии.
После выявления первых признаков зарождающегося дефекта интервал времени между двумя измерениями необходимо сократить. В зависимости от локализации дефекта интервал времени между замерами сильно меняется. Он минимален при дефектах тел качения, которые могут развиваться очень быстро.
Подшипник подлежит замене или ежедневному наблюдению при наличии в нем двух сильных дефектов.
Для обеспечения необходимой точности расчета остаточного ресурса и даты проведения ремонта в расчетах необходимо применение математических моделей с порядком не ниже третьего - четвертого. Если вспомнить, что один подшипник описывается не менее, чем десятком математических моделей, то становятся представимыми те математические затраты, необходимые для корректного прогнозирования параметров эксплуатации подшипника качения. А таких подшипников на предприятии в работе может одновременно находиться в работе несколько тысяч.
Процедура контроля состояния многих подшипников на предприятии становится возможной только при использовании компьютеров, в которых создаются и работают базы данных по подшипникам и современные экспертные системы диагностики.
Приборы нашего производства для диагностики подшипников качения
- ДПК-Вибро – компактный виброметр, прибор оперативной диагностики подшипников качения
- Vibro Vision-2 – анализатор вибросигналов с расширенными функциями диагностики подшипников качения